10.4.1.2 Maschinenaufbau der WPA im Detail
Die WPA unterteilt sich in zwei große Bereiche: das Wet End und das Dry End.
Abb. 10.4.1.3: Aufbau einer Wellpappenanlage (Quelle: Fa. BHS) – das Wet End
Zum Wet End gehören:
• Abrollung und Splicer, Single Facer
• Vorheizer
• Riffelwalzenstation
• Kaschierstation
• Auftragswerk für Klebstoff
• Brücke
• Abrollungen für die Außenbahnen
Abb. 10.4.1.4: Aufbau einer Wellpappenanlage (Quelle: Fa. BHS) – das Dry End
Zum Dry End gehören:
• Heiz- und Zugpartie
• Kurzquerschneider
• Schneid- und Rillstation
• Querschneider – Erzeugung der Abschlagslänge
• Ablage
Wet End, Abrollung und Splicer, Single Facer
Die Abrollung hat die Aufgabe, ein sicheres und ruhiges Halten der Papierrolle zu gewährleisten. Gleichzeitig wird eine konstante Bahnspannung erzeugt, indem die ablaufende Papierbahn abgebremst wird.
Abb. 10.4.1.5: Prinzip – Abrollung (Quelle: Eigene Darstellung)
Abb. 10.4.1.6: Blick auf Abrollung des Wellenstoffes (Quelle: Fa. BHS)
Die Konstruktion der Abrollung ist für Decken- und Wellenpapiere gleich. Es kommen bei großen Anlagen aufgrund des hohen Gewichtes der Rollen und zugunsten eines schnellen Rollenwechsels achslose Abrollungen zum Einsatz. Dabei dringen zwei Zentrierkonen seitlich in die Hülse ein und fixieren die Rolle. Dies geschieht in den meisten Fällen durch einen formschlüssigen Kontakt zwischen Hülse und Spannkonen. Durch das Aufspannen der Spannkonen in der Hülse wird es ein kraftschlüssiges Fügen.
Splicer
Der Splicer dient zum sicheren Ankleben der neuen Rolle (Bahn) an die ablaufende Rolle (Bahn) – und zwar möglichst bei voller Produktionsgeschwindigkeit. In Abhängigkeit der Maschinenendgeschwindigkeit kann vor dem Splicen die Maschinengeschwindigkeit reduziert werden.
Abb. 10.4.1.7: Prinzip – Splicer (Quelle: Eigene Darstellung)
Der Rollenwechsel (Spleißen) erfolgt automatisch. Dies geschieht über eine zweite Abrollung, in der die neue Rolle für den Rollenwechsel vorbereitet ist. Die neue Rolle ist mit einem zweiseitigen Klebeband versehen. Beim Wechseln wird die neue Rolle auf die Geschwindigkeit der ablaufenden Rolle beschleunigt. Damit werden Spannungsspitzen vermieden. Die Papierbahn wird oberhalb der Abrollung in Schlaufen geführt. Damit entsteht für das Spleißen eine Pufferzone. Die Absenkung der Maschinengeschwindigkeit, gepaart mit der überschüssigen Papierbahn in der Pufferzone, ergibt die Zeit für den Rollenwechsel.
Nach dem Spleißen der neuen Rollenbahn an die ablaufende Rollenbahn wird die Bahn der alten Rolle abgeschlagen, und die Wellpappenanlage wird wieder auf Geschwindigkeit gefahren. Ihr Arbeitstempo war, wie bereits erwähnt, zuvor etwas verlangsamt worden.Die Abrollung hat somit neben der Regulierung der Bahnspannung auch die Funktion der Rollenbeschleunigung im Rollenwechselvorgang.
Wet End, Vorbereitung der Bahnen (Konditionierung des Papiers)
Die Decken- und Wellenbahnen müssen vor ihrer Verarbeitung, sprich dem Riffeln und Verkleben, vorbereitet werden. Es ist wichtig, dass beide Bahnen vergleichbare Ausgangswerte in Bezug auf Temperatur und Feuchtegehalt haben. Diese Vorbehandlung nennt man Konditionierung; sie garantiert, dass beide Bahnen beim Verarbeitungsprozess dimensionsstabil bleiben.
Wir unterscheiden:
– Aufheizen der Deckenbahn
– Vorbereitung der Wellenbahn
Vorheizer
Das Vorwärmen der Decken- und Wellenpapiere erfolgt über einen Vorheizer.
Abb. 10.4.1.8: Prinzip – Vorheizer (Quelle: Eigene Darstellung)
Beim Vorheizer handelt es sich um einen Trockenzylinder. Die Beheizung der Zylinder erfolgt mit Dampf. Der Dampfdruck kann dabei bis zu 10 bar betragen. Der über einen Dampfkopf in den Zylinder einströmende Dampf unterliegt aufgrund des größeren Durchmessers des Zylinders zur Dampfleitung einer Druckänderung. Diese Druckänderung in Verbindung mit einer Abkühlung der Zylinderoberfläche durch das Papier lässt den Dampf kondensieren. Die dabei abgegebene latente Wärme führt zur Beheizung des Zylinders. Das sich bildende Kondensat wird über einen Siphon durch den Dampfkopf wieder aus dem Zylinder abgeleitet. Über dieses Prinzip werden auf der Zylinderoberfläche Temperaturen bis zu 190°C erzielt. Dampfköpfe sind Drehdurchführungen für den Anschluss von statischen Leitungen an rotierende Anlagensysteme wie zum Beispiel Zylinder, in die der Dampf hinein- und das Kondensat herausgeleitet werden.
Abb. 10.4.1.9: Aufbau eines Trockenzylinders mit Dampfkopf und stehendem Siphon (Quelle: Eigene Darstellung)
Durch den Kontakt des Papiers mit der Zylinderoberfläche wird die Wärme ins Rohpapier übertragen und damit die Bahn erwärmt. Der Grad der Erwärmung kann durch den Umschlingungswinkel der Bahn um den Zylinder verändert werden. Mit zunehmender Temperaturerhöhung in der Papierbahn verändert sich auch der Trockengehalt des Papiers. Die Ausgangsfeuchte im Papier von durchschnittlich sieben Prozent sinkt.
Abb. 10.4.1.10: Prinzip – Vorheizer mit Verstellung der Umschlingung (Quelle: Eigene Darstellung)
Das Aufwärmen der Papierbahn dient insbesondere zur:
– weiteren Verkleisterung des Klebstoffes
– Minimierung von Spannungen im Papier zwischen Decken- und Wellenbahn
Üblicherweise wird die Deckenbahn reguliert erwärmt. Es ist aber auch möglich, Deck- und Wellenbahn reguliert zu erwärmen, wenn Feuchtigkeitsunterschiede vorhanden sind. Die erreichte Temperatur auf der Deckenbahn bestimmt dabei den Aufheizungsgrad der Wellenbahn.
Die Vorbereitung der Wellenbahn ist im Gegensatz zur Deckenbahn aufwendiger. Über die Funktion des Aufwärmens der Papierbahn hinaus ist der Vorheizzylinder auch noch angetrieben. Durch den angetrie-benen Vorheizzylinder wird ein Überschuss an Papier der Riffelpartie zugeführt.
Größere Bedeutung als das Aufheizen der Wellenbahn hat die Regulierung der Feuchte. Der Riffelprozess läuft bei einer Feuchte von 7 bis 9 Prozent optimal ab. Da ein Teil der Ausgangsfeuchte des Rohpapiers durch das Vorheizen verdampft, ist eine Nachbefeuchtung notwendig.
Dabei werden die Rohpapiere nach ihren holzhaltigen Anteilen unterschieden:
• Altpapier-Wellenstoff: 6 bis 8 Prozent
• Halbzellstoff-Wellenstoffe: 8 bis 10 Prozent
Das Sprühsystem wird beidseitig angewandt und ist in Zonen (Kammern) aufgeteilt. Entsprechend dem Feuchteprofil der Papierbahn wird die Bahn besprüht. Dies geschieht durch eine Sprühdampfbehandlung. Durch Einbringen von Feuchtigkeit vermindert sich die Steifigkeit des Papiers. Die Dehnbarkeit wird erhöht, und es werden innere Spannungen im Papier abgebaut. Diese Effekte wirken sich beim Umformungsprozess wie auch bei der Verklebung der einzelnen Bahnen positiv aus. Für eine gute Verklebung ist eine Steuerung der Penetration des Klebstoffes in das Papier hinein entscheidend. Mit einer optimalen Feuchte an der Papieroberfläche kann das Eindringen des Klebstoffes gesteuert werden. Es ist wichtig, dass der Klebstoff an der Papieroberfläche verbleibt und nicht in das Papier wegschlägt.
Abb. 10.4.1.11: Feuchtigkeitsverteilung im Papier während der Vorkonditionierung (Quelle: Eigene Darstellung)
Einseitige Maschine – Modul Facer
In der einseitigen Wellpappenmaschine erfolgt einerseits die Umformung von der glatten zur gewellten Bahn (das Riffeln), andererseits wird diese nun gewellte Bahn mit der ersten Deckenbahn verklebt.
Die einseitige Maschine ist als das Kernstück der gesamten Wellpappenanlage anzusehen und umfasst folgende Bereiche:
• Formen der Wellenbahn durch mit Dampf beheizte Riffelwalzen
• Auftrag des Klebstoffes auf die Wellenspitzen
• Ankleben einer Deckenbahn auf die einseitige Wellpappe
Abb. 10.4.1.12: Prinzip – einseitige Maschine mit Anpressband und die Herstellung von zwei Wellentypen (Beispiel B- und E-Welle, Quelle: Fa. BHS)
Wet End – das Riffeln von Papier
Das Ziel beim Riffeln liegt darin, das Papier bei hoher Maschinengeschwindigkeit möglichst schonend und mit geringer Beanspruchung auf Zug, Druck und Biegung umzuformen. Wichtig ist, dass die Formbeständigkeit bis zur Fixierung an die Deckenbahn durch Klebstoff erhalten bleibt.
Abb. 10.4.1.13: Riffelvorgang im Detail – Schema (Quelle: Eigene Darstellung)
Durch den Riffelprozess wird eine vertikale Linienkraft von bis zu 100 kN/m auf das Wellenpapier ausgeübt. Gleichzeitig erfolgt eine Übertragung des Drehmomentes von der unteren angetriebenen Riffelwalze über das Papier auf die obere Riffelwalze, die nicht angetrieben ist. Dadurch kommt es zu einer irreversiblen Änderung des Papiergefüges und der damit verbundenen Ausformung der Welle. Gleichzeitig führt dieser Vorgang zu einer Dickenreduzierung der Papierbahn. Das Riffeln bedeutet eine Verformung des Papiers. Im Papier muss eine ausreichende Elastizität vorhanden sein, um eine zerstörungsfreie Formbarkeit des Papiers zu ermöglichen.
Die Elastizität und Formbarkeit werden durch in der Papierfaser befindliche Bestandteile von Lignin (Holzanteile) und Zellulose (holzfreie Anteile) hervorgerufen. Diese Bestandteile verhalten sich thermoplastisch unterschiedlich. Das thermoplastische Verhalten von Stoffen wird bestimmt durch Wärme und Feuchtigkeit. Bei Lignin ist die thermoplastische Temperatur bei 120° und damit höher als bei Zellulose. Die Feuchtigkeitsaufnahme ist dafür bei Zellulose höher als bei Lignin. Damit erfolgt bei Abkühlung oder Entzug von Feuchtigkeit der Erstarrungspunkt bei Lignin eher als bei Zellulose. Den Erstarrungspunkt unter den Bedingungen von Temperatur unter Einfluss von Feuchtigkeit wird „Glasübergangstemperatur“ genannt. Deshalb sind für die Wellenbildung eine entsprechend hohe Temperatur und ein definierter Feuchtigkeitsgehalt im Papier entscheidend.
Beim Einlaufen des Papiers zwischen die beiden Riffelwalzen hat die Papierbahn (durch den angetriebenen Vorheizer) eine höhere Geschwindigkeit als die Riffelwalzen. Damit entsteht ein Materialüberschuss bei der Wellenbahn im Verhältnis zur Deckenbahn, das entspricht dem sogenannten Einzugsfaktor bei der Riffelung. Unter dem Einzugsfaktor versteht man das Verhältnis der Länge eines Abschnitts der gewellten Bahn zur Länge des Abschnitts nach dem Herausziehen der Wellen, also des Abschnitts im planliegenden Zustand. Er ist wichtig, um den Wellenrohpapierbedarf für die Produktion einer Wellpappe zu berechnen.
Umschlingungswinkel (Theta ?)
Unter dem Umschlingungswinkel versteht man die „Summe aller Winkel“, die sich durch den Kontakt zwischen dem Papier und der Riffelwalze ergeben. Der Umschlingungswinkel ist von der Anzahl der Zähne, die vom Papier berührt werden, und dem Riffelprofil abhängig. Die sich daraus ergebene Riffelgeometrie bestimmt das Wellenprofil.
Abb. 10.4.1.14: Einlauf des Rohpapiers in die Riffelzone (Modell) (Quelle: Eigene Darstellung)
Einzugsfaktor
Durch den Wellungsvorgang erfolgt im Gegensatz zu den flachen Bahnen (Wellen- und Deckenrohpapier) ein Mehrverbrauch an Papier bei der Wellenbahn. Dieser zusätzliche Verbrauch wird durch den Einzugsfaktor ausgedrückt. Er hängt im Wesentlichen vom Wellenprofil ab und wird vorwiegend als materialökonomische Kenngröße verwendet. In der Praxis bestehen Differenzen zwischen den theoretischen und den tatsächlichen Einzugsfaktoren. Diese rühren hauptsächlich aus dem Verhalten des Wellenpapiers bei der plastischen Verformung her.
Die Einflussgrößen dabei sind:
• die geometrischen Verhältnisse zwischen der unteren Riffelwalze und der oberen Anpresswalze,
• die elastischen Dehnungen des Deckenpapiers unter Zugbeanspruchung,
• die partiell entstehende Feuchtigkeitszunahme beim Auftrag des Klebstoffes und
• die Schrumpfungsvorgänge beim Trocknen der Papierbahn innerhalb der Riffelwalzen.
Berechnung des Einzugsfaktors:
Die praktische, einfache Berechnung für die Beurteilung des Mehrverbrauchs bei der Wellenbahn ist:
Abb. 10.4.1.15: schematische Darstellungen von Wellenhöhe und Wellenteilung (Quelle: Eigene Darstellung)
Für eine überschlägige, einfache Berechnung wird die Wellenhöhe durch die Wellenbreite geteilt. Somit ergibt sich ein Faktor, mit dem der Materialeinsatz der Deckenbahn multipliziert wird und sich die größere benötigte Wellenmenge berechnet. Eine umfangreichere und genauere Berechnung werden durch Arbeitsvorbereiter vor Herstellung der Wellpappe errechnet und den Maschinenführern in absoluten Papiermengen vorgegeben.
Abb. 10.4.1.16: Einzugsfaktoren für übliche Wellpappenprofile (Quelle: Eigene Darstellung)
Abb. 10.4.1.17: Übersicht nach Wellenprofilen (Quelle: Eigene Darstellung)
Wie aus der Tabelle zu ersehen ist, muss im Riffelspalt für das jeweilige Riffelprofil eine entsprechend größere Menge an Papier zugeführt werden. Die richtige Geometrie ist entscheidend für die Ausformung der Welle.
Die Beanspruchung des Papiers bei der Riffelung
Beim Umformungsprozess (der Wellenbildung) wird das Papier starken Zug-, Druck-, Biege- und Scherbeanspruchungen ausgesetzt. Diesen kann es nur standhalten, wenn es eine bestimmte Temperatur und Feuchte aufweist. Sonst kann es zu Wellenbrüchen kommen.
Abb. 10.4.1.18: Beanspruchung des Wellenpapiers am Zahnkopf (Quelle: Eigene Darstellung)
Die einzelnen Beanspruchungen führen zu hohen Belastungen im Papier. Nur durch das Einbringen von Temperatur und Feuchte wird die Elastizität des Papiers erhöht und es kann ein zerstörungsfreier Umformungsprozess ablaufen. Der Formungsprozess der Welle hängt weiter von der Geometrie der Riffelwalzen, ihrer Oberflächenbeschaffenheit, der Maschinengeschwindigkeit und natürlich den bereits beschriebenen Eigenschaften im Papier ab. Nachfolgend werden die einzelnen Belastungsarten beschrieben.
Zugbeanspruchung
Beim Einzug der flachen Papierbahn in den Riffelspalt erfährt die Papierbahn aufgrund der Wegdifferenz von Wellenberg zu Wellenberg eine Verringerung der Geschwindigkeit in horizontaler Richtung – die Bahn wird abgebremst. Durch die gleichmäßige Winkelgeschwindigkeit der Riffelwalzen und die höhere Zufuhrgeschwindigkeit der flachen Papierbahn in den Riffelspalt entstehen Reibungskräfte, die die Zugspannung im Einlaufspalt erhöhen. Diese Erscheinung (Relativbewegungen) ist innerhalb des Riffelvorgangesweitestgehend beendet, wenn sich das Papier den Riffelwalzenzähnen vollständig angepasst hat.
Die Biege- und Druckbeanspruchung
Zusätzlich zu den Zugbeanspruchungen treten während des Riffelns Biegespannungen an den Riffelzähnen und Druckbeanspruchungen zwischen den Riffelwalzen auf. Der Grund dafür ist der ausgeübte Anpressdruck der Riffelwalzen auf das Papier. Bei der Umschlingung des Papiers um den Riffelzahn wird die äußere Lage des Papiers gedehnt und die innere Lage gestaucht.
Belastung auf das Papier durch Biegespannung
Das Papier wird in der Außenlage über sieben Prozent gedehnt. Unter Vernachlässigung von Unregelmäßigkeiten in der Faser- und Blattstruktur ist in der Innenlage damit eine Stauchung auch um etwa sieben Prozent zu vermuten. Im Papierquerschnitt betrachtet ergibt sich eine Addition beider Biegespannungen (Dehnung + Stauchung) auf eine 14-prozentige Änderung der Papierdimension. Das Papier kann dieser extremen Belastung nur deshalb standhalten, weil es, aufgrund seines Feuchtegehaltes und der eingebrachten Temperatur, ein viskoelastisches Verhalten ausweist.
Belastung auf das Papier durch Druckspannung
Um ein Zurückziehen des Wellenstoffs aus der Riffelzone zu verhindern, wird ein bestimmter Liniendruck zwischen den Riffelwalzen eingestellt. Dies geschieht unter Beachtung der Papierbahndicke. Damit sollen die Zerstörung des Papiers beim Riffelprozess vermieden und das Auftreten von Wellenfehlern verhindert werden.
Wellpappenfehler
Deformierte – schrägliegende – Welle
Die Qualität der Wellenprägung ist deutlich zu erkennen, wenn man einen scharfen Schnitt durch das Wellpappen-Profil macht. Bei Betrachtung des Querschnitts erkennt man nun die schrägliegende Welle.
Abb. 10.4.1.19: Wellenausbildung – normal und schief (deformiert) (Quelle: Eigene Darstellung)
Die Ursachen können sein:
• Die Riffelwalzen stehen nicht parallel.
• Die Anpresswalze am Klebstoffwerk quetscht die Welle.
• Es liegen falsche Einstellungen beim Transport des Verbundes vor – zum Beispiel zu hohe Druckbelastungen in der Zug- und Heizpartie.
• Das Wellenpapier ist nass.
Beschädigte Wellen
Wellenbruch
Abb. 10.4.1.20: prinzipielle Darstellung von Wellenbrüchen (Quelle: Eigene Darstellung)
Die Ursachen hierfür können sein:
• Papier ist beim Umformen zu trocken oder
• Papier ist zu feucht.
Durchschnittene Riffelung
Die Wellpappe wurde während der Riffelung einseitig durchschnitten. Die Ursachen für diesen Wellpappenfehler können sein:
• fehlende Parallelität der Riffelwalzen oder
• ungleichmäßiges Papierquerprofil (mA, Dicke).
Die Wellpappe wurde während der Riffelung beidseitig durchschnitten. Die Ursachen sind:
• eine falsche Bombage der Riffelwalzen oder
• ungleichmäßiges Riffelprofil.
Bombierte Walzen sind im Walzenumfang in der Mitte dicker als an den Rändern. Damit bleiben die Walzen trotz des Druckes zueinander parallel.
Risse in der geriffelten Bahn
Die Ursachen sind:
• übermäßige Spannungen in der Wellenbahn; starke Abbremsung,
• Riffelprobleme durch falsche Tiefeneinstellung,
• neue Riffelwalzen,
• fehlende Parallelität der beiden Riffelwalzen zueinander oder
• nicht adäquate Papierqualität: zu wenig Zugfestigkeit, ungeeignete Papierstärken (mA zu hoch/ zu niedrig).
Hoch-Tief-Erscheinung
Fehler in der Formbeständigkeit lassen sich an den sogenannten Hoch-Tief-Erscheinungen erkennen. Deutlich werden diese Fehler in der Verminderung des Flach-Stauch-Widerstands der Wellpappe.
Abb. 10.4.1.21: Hoch-Tief-Effekte (Quelle: Eigene Darstellung)
Wet End – Aufbau der Riffelwalzen
Riffelwalzen werden, um eine Durchbiegung der Walzen zu vermeiden beziehungsweise eine exakte Parallelität der Walzen über die gesamte Breite zu garantieren, bombiert (siehe Abb. 10.4.1.23). Die Bombage beträgt je nach Arbeitsbreite zwischen 0,2 und 1,6 Millimeter. Damit ist ein konstanter Liniendruck über die Breite gegeben. Die Walzen sind verchromt, sodass ihre Oberfläche glatt ist. Die Riffelwalzen werden wie die Vorheizer mit Dampf beheizt.
Abb. 10.4.1.22: Riffelwalzenpaar (Quelle: Eigene Darstellung)
Wenn Walzenzylinder in der Mitte dicker sind als an den äußeren Seiten, bezeichnet man das als Bombage. Die schematische Darstellung zeigt überzeichnet, warum dies geschieht. Die Bombage der Walzen sorgt im Arbeitsprozess für einen gleichmäßigen Walzenspalt.
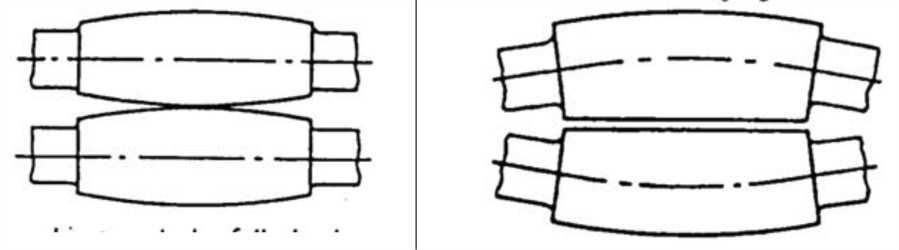
Abb. 10.4.1.23: Bombierte Walzen ohne und mit Belastung im Arbeitsprozess (Quelle: Eigene Darstellung)
Arbeitsweise der Wellpappenanlage: Wet End – Bauarten von Riffelwalzensystemen
Um den Wellenstoff an den Riffelwalzen bis zur Fixierung mit der Deckenbahn zu halten, werden verschiedene Konstruktionen angewendet:
• Wellpappenmaschinen mit Führungsblechen,
• führungslose Wellpappenmaschinen, die mit Unterdruck arbeiten und
• führungslose Wellpappenmaschinen, die mit Überdruck arbeiten.
Der Einsatz der verschiedenen Systeme hängt im starken Maße von den konstruierten Geschwindigkeiten der Anlage ab. Das System der Wellpappenmaschinen mit Führungsblechen ist in älteren und langsameren Wellpappenanlagen im Einsatz. Das Führungsblech ist auf einen Abstand von 0,3 mm eingestellt.
Abb. 10.4.1.24: Riffelwalzen mit Führungsblech (Quelle: Eigene Darstellung)
Schnelle Wellpappenanlagen arbeiten ohne Führungsblech – man spricht in diesem Fall von einem führungsblechlosen Maschinensystem („fingerless single facer“). Solche Maschinen arbeiten mit Druck- und Vakuumtechnik.
Überdruck-Maschinen
Diese arbeiten mit einer im Single Facer integrierten Überdruck-Kammer. Das Anpressen der Wellenbahn an die Riffelwalze erfolgt mithilfe einer Druckdifferenz. Beim Überdrucksystem befindet sich das Papier vom Riffelspalt (obere und untere Riffelwalze) bis zum Anpressspalt (untere Riffelwalze und Anpresswalze) in einer Überdruckkammer. Die Schwierigkeit in diesem System besteht darin, dass das Klebstoffauftragswerk mit in der Überdruckkammer sein muss, was die Dichtheit des Systems erschwert.
Unterdruck-Maschinen
Bei den Unterdruck-Maschinen gibt es zwei konstruktive Lösungen:
• erzeugtes Vakuum aus der Riffelwalze oder
• angelegtes Vakuum in einer Kammer, welches gegen die Riffelwalzen wirkt.
Bei der ersten Konstruktion wird das Vakuum von den Stirnseiten der Riffelwalze über axiale Bohrungen über Nuten an die Oberfläche der Walzen gebracht. In der zweiten Konstruktionsvariante wird durch die Unterdruckzone, die zwischen dem Wellenpapier und der unteren Riffelwalze ausgebildet ist, das gewellte Papier formtreu gegen die Oberfläche der Riffelwalze gepresst. Der Unterdruck wird in beiden Fällen durch ein Sauggebläse erzeugt.
Arbeitsweise der Wellpappenanlage: Wet End – Klebstoffauftrag
Zum Verbinden der geriffelten Papierbahn mit dem Deckenpapier (Fixierung) ist ein Klebevorgang notwendig. Dieser Verfahrensschritt ist ein wichtiger Bestandteil der einseitigen Wellpappenmaschine. Die Riffelung sowie das Verkleben erfolgen unmittelbar nacheinander im gleichen Maschinenbereich an den Riffelwalzen. Technologisch erfolgt die Verklebung der Wellenbahn und der Deckenbahn in einer 180°-Drehung um die untere Riffelwalze. Der Klebstoff wird bei rund 90° aufgetragen. Der gesamte Vorgang dauert wenige Millisekunden.
Abb. 10.4.1.25: schematische Darstellung des Klebevorgangs (einseitige WPA, Quelle: Fa. BHS)
Abb. 10.4.1.26: prinzipielle Darstellung – Auftragen des Klebstoffs (Quelle: Fa. BHS)
Anpressen und Verkleben
Durch das Anpressen der ebenen Deckenbahn mit der benetzten gewölbten Fläche der Wellenbahn wird ein Teil des Klebstoffs aus der Kontaktzone verdrängt, und es bilden sich Dickschicht- und Dünnschichtbereiche.
Abb. 10.4.1.27: Darstellung – Anpresszone (Quelle: Eigene Darstellung)
Abb. 10.4.1.28: Ablauf der Verklebung zwischen Wellen- und Deckenpapier: Hier entstehen zunächst Dünnschicht- (1) und Dickschichtbereiche (2) des Klebstoffs. Ein Teil des Klebstoffs wird beim Anpressen durch das Papier aufgesaugt. Das vierte Teilbild zeigt die Wellpappe nach dem Aushärten. (Quelle: Eigene Darstellung)
Der Klebstoff unterliegt in der Phase der Verbindung der beiden Bahnen zwei entscheidenden Bedingungen:
1. Der Klebstoff muss bis zum Anpressen der Deckenbahn an die mit Klebstoff versehene Wellenbahn eine ausreichende Viskosität behalten. Die Penetration des Klebstoffs soll in beiden Bahnen möglichst gleichmäßig sein. Dabei muss aber berücksichtigt werden, dass die Viskositätdes Klebstoffs beim Aufbringen auf das Wellenpapier sprunghaft ansteigt. Das ist die Folge eines einsetzenden Entwässerungsvorganges beim Klebstoff durch die Saugwirkung des Papiers und die Wärme der Riffelwalze.
2. Weiterhin soll der Klebstoff bis zum Aufbringen der Deckenbahn eine ausreichende Klebekraft haben, um einen festen Verbund zu gewährleisten.
Das Verhalten des Klebstoffs zwischen Auftrag und Verkleben mit der Deckenbahn ist gekennzeichnet durch die Zeit, in der die Stärke (als Hauptbestandteil des Klebers) das in sich gespeicherte Wasser abgibt. Die Steuerung des Kapillardruckes (Saugwirkung des Papiers) erfolgt durch die Papiereigenschaften. Im Klebstoff bestimmen die verwendete Stärke, ihr Aufschlussgrad der Stärke und die beigegebenen Füllstoffe das Klebeverhalten und die offene Zeit des Klebers. Die Verbundfestigkeit wird, neben den Papiereigenschaften und der Klebstoffgüte, von der Größe der Klebefläche und dem ausgeübten Druck auf die Klebestelle bestimmt.
Abb. 10.4.1.29: optimale Verklebung zwischen Wellen- und Deckenpapier (Quelle: Eigene Darstellung)
Klebstoff
Mit zunehmender Leistungssteigerung der Verarbeitungsmaschinen haben sich die Technologie sowie der Einsatz und die Zusammensetzung des Klebemediums geändert. Während früher die Deckenbahn vollflächig mit Klebstoff bestrichen wurde, werden heute nur die Wellenberge mit Klebstoff benetzt. Dieser technologische Wandel bringt hohe ökonomische Einsparungen.
Der Klebstoff wird aus Stärke hergestellt. Dabei werden in Deutschland für Klebstoffe in der Wellpappenindustrie hauptsächlich Mais-, Weizen- und Kartoffelstärke verwendet.
"In Deutschland wird Leim auf Basis von Mais-, Weizen- oder Kartoffelstärke bzw. Kombinationen daraus verwendet. Stärkeleim hat eine geringe Fließfähigkeit (Viskosität), kann aber trotzdem mit modernen Leimwerken gleichmäßig über die ganze Arbeitsbreite der Wellpappenmaschine aufgetragen werden.“ (Quelle: https://www.wellpappe-wissen.de/wissen/wellpappe/bauprinzip/verklebung.html)
Abb. 10.4.1.30: Stärketyp und Stärkekörner (Quelle: Fa. Cargill)
Stärke ist ein makromolekularer Naturstoff, der aus Glukose synthetisiert wird und beim pflanzlichen Stoffwechsel als Energiespeicher dient. Wenn die Stärke aus den Pflanzenteilen als weißes Pulver isoliert ist, wird sie als native Stärke bezeichnet. Native Stärke besteht aus harten – in Wasser unlöslichen – Körnern, deren Größe und Form von der Pflanzenart abhängig ist. In der Wellpappenindustrie wird vorwiegend Maisstärke verwendet.
Stärkeaufbereitung
Die Stärke wird in kaltem Wasser angesetzt, danach wird die Slurry (flüssiges Medium versetzt mit festen Substanzen) erhitzt. Ab einer Temperatur von rund 80°C beginnt das Korn zu quellen und bei weiterer Temperaturzunahme (85 bis 105°C) zu verkleistern. Bei der Verkleisterung kommt es zu einer Volumenvergrößerung des Stärkekorns. Die Verkleisterung kommt nur dann zustande, wenn neben der Temperatur auch die notwendige Wassermenge für die Quellung vorhanden ist. Das hängt mit dem Wasseraufnahmevermögen des Korns zusammen. Aus diesem Grund sollte der Feststoffgehalt nicht über 30 Prozent liegen.
Abb. 10.4.1.31: verschiedene Zustände der Stärke vor und nach der Verkleisterung (Quelle: Eigene Darstellung)
Bei der Verkleisterung ist infolge der starken Quellung ein rascher Anstieg der Viskosität vorhanden. Sie ist so hoch, dass ein Feststoffgehalt von 30 Prozent eine pastöse Konsistenz hervorbringt. Um den Klebstoff pumpfähig zu machen, sind entweder Ansätze mit geringerem Feststoffgehalt vorzunehmen oder eine Nachverdünnung notwendig. Zu niedrige Feststoffgehalte führen zu Trocknungsproblemen und Leistungseinbußen der Anlage.
Verklebung
Unzureichende beziehungsweise schlechte Verklebung
Abb. 10.4.1.32: Beispiel einer schwachen Verklebung – Klebstoffauftrag zu mager (Quelle: Eigene Darstellung)
Bei einer unzureichenden Verklebung ist entweder die Klebstoff-Auftragsmenge zu gering oder der Klebstoff-Film ist ungleichmäßig verteilt. Auch die Eindringtiefe des Klebstoffs in das Papier (Penetration) kann zu gering sein, sodass der Gelierungsprozess nicht stattfindet und die Klebkraft des Klebstoffs sinkt.Typische Merkmale dieser Erscheinung sind weiß aussehende mehrlagige Streifen auf den Wellenkronen.
Wie erkenne ich eine schlechte Verklebung?
• Bahnen lassen sich ohne nennenswerten Kraftaufwand trennen.
• Bei der Trennung der Bahnen entsteht fast kein Faserabriss.
• Es zeigen sich sichtbare „Markierungen“ (Streifen) durch Anpresswalzen.
Durch eine „zerstörende Prüfung“ – das Abschälen einer Deckenbahn von der Wellpappe – kann festgestellt werden, ob der Klebstoffauftrag ausreichend war und somit eine gute Verklebung vorliegt.
Abb. 10.4.1.33: Beispiel einer einwandfreien Verklebung (Quelle: Eigene Darstellung)
Woran erkenne ich eine gute Verklebung?
• An den Verbindungsstellen findet sich reichlich Faserabriss.
• Deutliche Abrissmarkierungen sind zu sehen.
Klebstoffauftrag zu reichlich
Der Klebstoff ist niedrigviskos und kann 75 bis 85 Prozent Wasser enthalten. Bei einem Mehrauftrag an Klebstoff mit dieser hohen Feuchtigkeit nimmt die Feuchte in der Wellpappe sprunghaft zu. Da diese Er-scheinung partiell (Wellenberge und Umgebung) auftritt, führt dies zu höheren Spannungen im Verbund. Das Verziehen der Wellpappe-Bogen ist die Folge.
Wie erkenne ich einen zu reichlichen Klebstoffauftrag?
• Die Klebstoff-Fuge ist unverhältnismäßig breit, es zeigt sich ein waschbrettähnliches Erscheinungsbild.
• Die Wellenkronen weichen auf.
• Der Gelierungsprozess des Klebstoffs ist erschwert.
Arbeitsweise der Wellpappenanlage: Wet End – Brücke
Die Brücke ist das Verbindungsglied zwischen der einseitigen Wellpappenmaschine und der Kaschieranlage. Die Wellpappe kann sich in dieser Zone den klimatischen Umgebungstemperaturen anpassen. Diese klimatische Anpassung ist wichtig, da durch das Aufheizen der Bahnen und die Einbringung hoher Feuchtigkeit Spannungen in der Wellpappe auftreten können. Diese Spannungen führen zu krummen Bogen (Warp). Die Brücke dient weiterhin als Transporteinrichtung, in der das produzierte Material gepuffert wird. Diese Pufferung wird dadurch erreicht, dass die Brücke eine niedrigere Produktionsgeschwindigkeit als die WPA hat. Der Hochtransport der einseitigen Wellpappe zur Brücke muss knickfrei erfolgen. Dort wird die einseitige Wellpappe in gleichmäßigen Schlaufen gelegt.
Abb. 10.4.1.34: schematische Darstellung einer Brücke (Quelle: Eigene Darstellung)
Die Brückenmengenregelung hält die Speichermenge auf der Brücke konstant. Dies geschieht durch Anpassung der Anlagengeschwindigkeit der einseitigen Gruppe(n).
Arbeitsweise der Wellpappenlage: Wet End – Verbinden der einseitigen Wellpappe mit der zweiten Außendeckenbahn
Der zweite Deckbogen wird ebenfalls vorkonditioniert, wie auch vorher die einseitige Wellpappe. Dabei handelt es sich ausschließlich um eine Wärmebehandlung. Diese Maßnahme dient zur Feuchtigkeits- und Temperaturangleichung der zweiten Deckenbahn. Danach erfolgt der gleichmäßige Auftrag des Klebstoffs über die Arbeitsbreite auf die Wellenspitzen der einseitigen Bahn(en). Die Anzahl der Klebstoffauftragswerke richtet sich nach der Anzahl der einseitigen Bahnen. Die Auftragswerke sind dabei übereinander angeordnet. Der Klebstoffauftrag erfolgt über eine Auftragswalze, die den Klebstoff aus einer Wanne schöpft. Eine weitere Walze entfernt dabei den überschüssigen Klebstoff. Es entsteht ein gleichmäßig eingestellter Film. Dieser Anlageteil wird als Kaschiermaschine bezeichnet und dient zur Aufbringung des Klebers und des Anklebens des zweiten Deckbogens.
Abb. 10.4.1.35: Prinzip – Ablauf im Kaschierwerk (Quelle: Eigene Darstellung)
Aufbau der Wellpappenanlage: Dry End, Heiz- und Zugpartie
Das Zusammenführen der Bahnen (einseitige Bahn(en) und Kaschierliner) erfolgt unmittelbar vor dem Einlaufspalt der Heiz- und Zugpartie, sodass die erste Berührung untereinander in einem Punkt erfolgt. Das Verkleben der Bahnen erfolgt im Bereich der Heizplatten durch die zugeführte Wärmeenergie und dem damit verbundenen Entzug der Feuchtigkeit. Der Transport der Wellpappe über die Heizplatten geschieht durch einen Transportgurt, der belastet ist. Das verdampfte Wasser muss vom oberen Gurt aufgenommen und danach abgeführt werden. Es handelt sich hierbei um eine Kontakttrocknung. Diese geschieht bei Geschwindigkeiten bis 300 m/min.
Die Trocknung umfasst im Wesentlichen zwei Aufgaben:
• die Bereitstellung der Wärme, die zum Verkleistern der noch nicht aufgeschlossenen nativen Stärke erforderlich ist, und
• der Trocknung beziehungsweise Entfernung des überschüssigen Wassers.
1 Heizplatten 2 Wellpappenbahn 3 Transportgurt (oben) 4 Belastungswalzen 5 verdampfendes Wasser
Abb. 10.4.1.36: Prinzip – Trocknung der Wellpappe (Quelle: Eigene Darstellung)
Die Heizplattenpartie wird in drei Gruppen aufgeteilt:
• Aufheizbereich,
• Verdampfungsbereich und
• Regelbereich für den Endtrockengehalt.
Mit diesem System werden auftretende Verspannungen in der Wellpappe abgebaut. Nach den Heizplatten folgt ein Untergurt und zieht die Wellpappenbahn mithilfe des Obergurtes durch die Maschine.
Planlage eines Bogens
Wenn die Wellpappenbogen nicht planliegen, werden diese kurz „krumme Bogen“ genannt. Diese können zu Problemen in der Verarbeitung führen. Die Wellpappe wölbt sich nach dem Austrocknen. Dies ist auf das unterschiedliche Dehnen und Schrumpfen der Außen- und Innenbahnen zueinander zurückzuführen. Ursachen dafür können sein:
• unterschiedliche Feuchtegehalte der einzelnen Bahnen sowie
• unterschiedliche Faserstoffzusammensetzung und Faserorientierung im Rohpapier.
Es gibt unterschiedliche Abweichungen von der Planlage. Wir kennen den Curl (Quer- und Längswölbung), die S-Wölbung und die Querverspannung (Propeller).
Querwölbung
Die Querwölbung entsteht durch zu hohe Feuchtigkeit in der Deckenbahn oder der einseitigen Wellpappe.
Querwölbung nach unten:
Dazu kommt es, wenn zu viel Feuchtigkeit in der unteren Deckenbahn ist:
• Die untere Deckenbahn ist nass oder kalt.
• Die obere Deckenbahn ist heiß oder trocken.
Querwölbung nach oben:
Dazu kommt es, wenn zu viel Feuchtigkeit in der einseitigen Wellpappe ist.
Längswölbung
Eine Längswölbung nach oben oder unten tritt in Papierlaufrichtung auf. Ursache ist eine zu hohe Spannung bei der Wölbung nach unten in die Deckenbahn. Diese dehnt sich während des Trocknens in der Heizpartie. Diese Deckenbahn zieht sich später wieder auf ihre ursprüngliche kürzere Länge zusammen, und die Wellpappe wölbt sich in die Laufrichtung abwärts. Für Längswölbungen ist auch das Dehnungsverhalten (Elastizität) des Papiers mitverantwortlich.
Längswölbung nach unten:
Dazu kommt es, wenn eine zu hohe Spannung in der unteren Deckenbahn herrscht.
• Die untere Deckenbahn hat sich während der Verklebung in der Heizpartie gedehnt.
• Beim Abkühlen nach dem Trocknungsprozess zieht sie sich zusammen.
Längswölbung nach oben:
Dazu kommt es bei übermäßiger Spannung in der Wellpappen-Rückseite.
Abb. 10.4.1.38: Darstellungen von Längswölbungen (Quelle: Eigene Darstellung)
S-Wölbung
Die S-Wölbung stellt sich quer zur Papierlaufrichtung ein. Die Ursache liegt in einem ungleichmäßigen Feuchtequerprofil in der einen oder anderen Papierbahn. Die trockenere Seite schrumpft.
Abb. 10.4.1.39: Darstellung einer S-Wölbung (Quelle: Eigene Darstellung)
Propeller-Wölbung
Bei der Propeller-Wölbung kommt zur S-Wölbung noch eine Verdrehung des Verbundes hinzu. Die Ursachen liegen im ungleichmäßigen Feuchtequerprofil der einen oder anderen Papierbahn. Diese können vom Rohpapier wie auch der Verklebung der Wellpappe herrühren. In den meisten Fällen liegen beide Faktoren vor. Hauptsächliche Probleme sind aber die zu große Abweichung in der Orientierung der Fasern und das Feuchtequerprofil des Papiers:
• ungleichmäßige Feuchtigkeit in den Papieren
• Quetschung der Pappe, zu hohe Zugspannung in der WPA
Abb. 10.4.1.40: Darstellung einer Propellerwölbung (Quelle: Eigene Darstellung)
Schlechte Planlage von Wellpappe ist in den meisten Fällen auf Feuchtigkeitsunterschiede in den Papieren zurückzuführen. Insbesondere die Deckenpapiere sind dabei die Hauptursache. Das kommt daher, dass für die Deckenpapiere hochwertigere Rohstoffe (mehr Langfaseranteile) eingesetzt werden und dass die Faserorientierung in einem Festigkeitsverhältnis von 1:2 (quer zu längs der Papierbahn) abweichen kann. Sehr entscheidend sind in diesem Zusammenhang auch die Winkel, in denen die Fasern im Papier liegen. Diese sollten nicht über 3° vom rechtem Winkel abweichen. Aber auch die eingestellte Trocknung zwischen einseitiger Wellpappe und zwei Deckbogen (Arbeit der Vorheizer) ist für Spannungen im Verbund von Bedeutung. Es ist zu ermitteln, ob diese Spannungsunterschiede aus dem Rohpapier kommen oder durch den Klebstoffauftrag.
Bedeutung beziehungsweise Einfluss der Planlage
Die Planlage ist entscheidend dafür, damit Wellpappe stabil auf dem Stapel liegt und sich problemlos auf Rollenbahnen transportieren lässt. Vor allem Feuchtigkeitsunterschiede in den Papieren können zu schlechter Planlage führen. Diese sorgt auch in der Weiterverarbeitung für Probleme.
Die Planlage ist auch entscheidend für:
• die Stabilität der Stapel und den problemlosen Transport auf den Rollenbahnen,
• die automatische Beschickung der Verarbeitungsmaschinen und damit die Produktivität der Anlage,
• den Durchlauf in den Verarbeitungsmaschinen und damit die Qualität der Weiterverarbeitung,
• das Entstehen von Passerungenauigkeit beim Drucken, Schlitzen und Stanzen,
• Störungen beim Verschließen,
• die Abnahme des Stauchwiderstandes und damit der Stabilität sowie
• das Ausmaß des Ausschusses.
Arbeitsweise der Wellpappenanlage: Dry End – Kurzquerschneider
Vor der Schneid- und Rillstation ist der Kurzquerschneider in der WPA platziert und kommt zum Einsatz beim Formatwechsel, um eine Lücke für die Aufnahme des neuen Formats zu schaffen. Weiterhin werden im Kurzquerschneider fehlerhafte Bahnabschnitte oder Splicer herausgeschnitten.
Abb. 10.4.1.41: Prinzip des Schneidvorgangs – quer (Quelle: Eigene Darstellung)
Der Schneidevorgang ist wie beim Querschneider. Beim Querschneider wird die für das entsprechende Format hergestellte Abschlagslänge erzeugt.
Arbeitsweise der Wellpappenanlage: Dry End – Schneid- und Rillstation
Die Rill- und Schneidstation ist eine Baugruppe der WPA. Hier beginnt die Verarbeitung der Formate. In ihr wird die Bahn in Längsrichtung entsprechend den vorgegebenen Abmessungen gerillt und geschnitten.
Abb. 10.4.1.42: Prinzip einer Rill- und Schneidstation (Quelle: Eigene Darstellung)
Zuerst wird die Bahn am Rand beschnitten und damit auf die gewünschte Breite gebracht. Das Beschneiden des Randes wird aus zwei Gründen durchgeführt:
– Es geht zum einen darum, Differenzen im Lauf zwischen Liner- und Wellenbahnen am Rand auszugleichen.
– Zum anderen ist der Beschnitt erforderlich, weil an den Rändern der Wellpappe aus klebtechnischen Gründen kein Klebstoffauftrag erfolgt. Deshalb wird die nicht verklebte Wellpappe am Rand abgeschnitten.
Nach dem Beschneiden des Randes wird die Bahn zur Vorbereitung der Biegestellen gerillt.
Abb. 10.4.1.43: Verarbeitung der Wellpappe, Schneiden und Rillen (Quelle: Eigene Darstellung)
Beim Rillen wird durch Verdichten und Verdrängen der Wellpappe eine Rille geformt. Dabei kommt es zur Aufspaltung des Verbundes. Dieses Verfahren wird dort angewandt, wo höhere Festigkeiten verlangt werden und eine höhere Toleranz in der Maßgenauigkeit zulässig ist. Für das Rillen muss der Werkstoff über eine ausreichende Elastizität verfügen. Diese wird hauptsächlich durch eine entsprechende Feuchte im Werkstoff und der Faserrichtung im Papier beeinflusst.
Abb. 10.4.1.44: Typen von Rillenkörpern (Quelle: Eigene Darstellung)
Beim Längsschneiden der fertigen Wellpappe werden zwei Schneideprinzipien angewandt. Dies ist zum einen der klassische Scherenschnitt, indem mit einem Ober- und einem Untermesser („Tellermesser“) die Bahnen getrennt werden. Zum anderen gibt es den Einmesserschnitt („Rasierklingenmesser“): Die Wellpappe liegt hier auf einer großen Fläche auf, und ein Obermesser taucht in den Verbund ein und läuft in eine Nut.
Das angetriebene Messer sorgt für einen sauberen und einwandfreien Schnitt. Die Anordnung gestattet eine schnelle und einfache Einstellung des Formates.
Abb. 10.4.1.45: Prinzip eines „Tellermessers“ und eines „Rasierklingenmessers“ (Quelle: Eigene Darstellung)
Abb. 10.4.1.46: Blick auf einen Einmesserschnitt mit Absaugung (Randbeschnitt) (Quelle: Eigene Darstellung)
Arbeitsweise der Wellpappenanlage: Dry End – Querschneider: Erzeugung der Abschlagslänge
Die in Längsrichtung gerillte und geschnittene Bahn wird auf einem Querschneider auf ein entsprechendes Format geschnitten.
Der nachfolgende Querschneider trennt nun die endlosen Bahnen quer zur Laufrichtung, also parallel zum Wellenverlauf. Er kann aus einer, zwei oder drei übereinanderliegenden Stationen bestehen. Beim Verlassen der Rill- und Schneideinheit werden die Bahnen je nach erforderlicher Schnittlänge auf die verschiedenen Stationshöhen gelenkt.
Abb. 10.4.1.47: Einzugssituation in den Querschneider (Quelle: Eigene Darstellung)
Die verwendeten Querschneider haben zwei synchron zueinander laufende Messer.
Abb. 10.4.1.48: Anordnung der Messer in der Quermesserpartie (Quelle: Eigene Darstellung)
Der Synchronlauf bedeutet, dass zum Zeitpunkt des Schnittes die Geschwindigkeit der Messertrommeln und der Wellpappenbahn exakt gleich ist. Damit wird ein rechtwinkliger und sauberer Schnitt erzielt.
Abb. 10.4.1.49: Verlauf der Messergeschwindigkeit bei einer Umdrehung (Quelle: Eigene Darstellung)
Arbeitsweise der Wellpappenanlage: Dry End – Ablage
Die Ablage ist das letzte Teilstück der WPA. Die Formate, die vom Ausgang des Querschneiders kommen, werden in diesen Bereich weitertransportiert. Dabei werden die Formate auf den jeweiligen Transportsektionen durch Bänder oder Gurte bis zur Ablagestation geführt. Eine Verringerung der Transportgeschwindigkeit in diesem Bereich führt zu einer Schuppung der einzelnen Bögen übereinander. Die Ablage einer WPA hat keine seitliche Ausrichtung, da mehrere Stapel nebeneinander liegen können.
Abb. 10.4.1.50: Prinzipielle Darstellung einer Ablage (Quelle: Eigene Darstellung)
Abb. 10.4.1.51: Blick auf den Transport, den fertigen Zuschnitt und den Stapel (Quelle: Eigene Darstellung)
Die Stapel werden im Allgemeinen durch ein Rollen- beziehungsweise Bandtransportsystem zur Weiterverarbeitung beziehungsweise zu einem Zwischenlager geleitet.