10.5.2 Produktionsmaschinen- und Anlagen für Industriesäcke
Abb. 10.5.2.1: Industriesäcke in verschiedenen Designs
Industriesäcke (siehe Band 1, Seite 168) werden heute im Füllgewichtsbereich von etwa fünf bis 50 Kilogramm beziehungsweise mit Füllvolumina von rund zwei bis 170 Litern produziert. Die Abgrenzung zum Beutel fällt zunehmend schwerer, da es einerseits immer kleinere Sackformate gibt, andererseits aber auch Gebinde auf Beutelmaschinen produziert werden, deren Füllvolumina im Bereich von Säcken liegen. Flexible Behälter für Füllgewichte, die über 50 Kilogramm (in der Praxis meist 200 bis 1000 Kilogramm) hinausgehen, werden als FIBC bezeichnet. FIBC steht für Flexible Intermediate Bulk Container, umgangssprachlich werden diese auch „Big Bag“ oder „Container Bag“ genannt. Sie werden hier nicht weiter betrachtet.
Säcke bieten den Vorteil eines universell einsetzbaren, einfach zu handhabenden, kostengünstigen und ökologischen Verpackungsmittels für die Verpackung von Schüttgütern. Ihre Hauptverwendungen liegen in den drei Produktsegmenten:
• Baustoffe (Zement, Kalk, Gips) und Mineralien
• Nahrungs- und Tierfuttermittel
• chemische Produkte
Hinzu kommen Sonder-Einsatzfälle wie Müllsäcke, Polstersäcke, Sandsäcke oder Säcke für die Umverpackung.
Im Verhältnis zum Füllvolumen benötigen Säcke nur eine sehr geringe Menge an Verpackungsmaterial. 50 Kilogramm Zement können mit 130 g Papier oder 90 g Polypropylen (PP) sicher transportiert werden, was einem Tara von 0,26 % beziehungsweise 0,18 % entspricht. In der Regel werden sie daher als Einwegverpackung verwendet. Gefüllte Säcke sind durch eine Person ohne Hilfsmittel handhabbar und daher nicht auf hoch entwickelte Transport- und Logistik-Infrastruktur wie Straßen, Schienennetz, Lagerhäuser, Silofahrzeuge, Hebezeuge, Gabelstapler, Paletten usw. angewiesen. Sie kommen dort zum Einsatz, wo Transport- und Umschlagsysteme auf der Basis von Großgebinden (wie zum Beispiel Big-Bags, Octabins oder Silo-Transportfahrzeugen) nicht vorhanden, nicht einsetzbar oder nicht wirtschaftlich sind:
• bei fehlender Verkehrs- und Logistik-Infrastruktur (zum Beispiel in sogenannten Entwicklungsländern),
• bei Unzugänglichkeit des Einsatzorts (beengte Altstadt, Bergbau, Bohrinseln) sowie
• im Falle des Bedarfs von Kleinmengen.
Octabins sind große achteckige Behältnisse für den Transport von Schüttgütern wie Granulat und Ähnliches.
Industriesäcke können als vorgefertigte Säcke bei einem Sackhersteller produziert, zum Verwender transportiert und dort befüllt oder Inline in einem Arbeitsgang aus Flach- oder Schlauchfolie hergestellt, befüllt und verschlossen werden. Dieser Prozess ist als FFS (Form, Fill, Seal) bekannt.
Abb. 10.5.2.2: Form-, Füll- und Verschließanlage (FFS, Quelle: Windmöller & Hölscher)
Als Fügeverfahren für Industriesäcke kommen Näh-, Kleb-, Schweiß- und Heißluft-Siegelprozesse zur Anwendung. Die Auswahl richtet sich primär nach dem Sackwerkstoff und dem Sacktyp, kann aber auch durch wirtschaftliche Überlegungen mitbestimmt werden. Auswahlkriterien für den Sackwerkstoff sind lokale Verfügbarkeit, die Anforderungen hinsichtlich des Produktschutzes, die Optik (das Aussehen) sowie die Kosten.
Papiersackherstellung
Papiersäcke sind weltweit verbreitet und nehmen mit einer Produktionsmenge von jährlich rund 25 Milliarden Stück weltweit den zweiten Platz hinter Bändchengewebesäcken (mehr als 40 Milliarden Stück pro Jahr) ein. Ihre Konstruktion (Format, Sackwandaufbau, Ausstattung) ist äußerst flexibel auf die spezielle Abfüll- und Logistiksituation anpassbar. Leistungsfähige Sackpapiere bieten hohe mechanische Festigkeit, hohe Abfüll-Leistungen durch gute Entlüftbarkeit sowie Rutschfestigkeit und Bedruckbarkeit. Darüber hinaus sind sie temperaturstabil, atmungsaktiv und hygienisch. Spezielle Ausrüstungen, wie zum Beispiel PE-Beschichtungen oder Folienzwischenlagen, erhöhen den Schutz des Produktes vor Umwelteinflüssen oder zielen auf eine attraktive Anmutung.
Papiersäcke werden aus nachwachsenden Rohstoffen hergestellt. Das gilt sowohl für die Sackpapiere als auch für die meisten Klebstoffe. Papiersäcke lassen sich daher nach ihrer Verwendung problemlos recyceln, kompostieren oder verbrennen und verhalten sich neutral in der CO2-Bilanz.
Es gibt eine ganze Reihe von Bauformen für Papiersäcke. Die größte Bedeutung am Markt haben geklebte Kreuzbodensäcke, gefolgt von genähten und geklebten Seitenfaltensäcken. Während Kreuzboden- und Nähsäcke sowohl in der Form von Ventil- als auch oben offenen Säcken auftreten, gibt es geklebte Seitenfaltensäcke (Pinch- und Rollbodensäcke) nur als oben offene Säcke.
Abb. 10.5.2.3: geklebte Seitenfaltensäcke (Pinchsäcke). Rollbodensäcke sehen im fertigen Zustand kaum anders aus. Die Kopfnaht wird nach der Befüllung jedoch fast immer genäht, bei Pinchsäcken geschieht dies nur manchmal.
Die Auswahl eines konkreten Sackkonzeptes richtet sich nach dem Füllprodukt und der vorhandenen Abfülltechnik, nach logistischen und Marketinggesichtspunkten, aber auch nach Kriterien der Sackproduktion – dazu zählen die Investitionshöhe für die erforderlichen Maschinen, die Stückkosten oder die Losgrößenflexibilität. Die Produktionsweise für geklebte Säcke ist stärker mechanisiert beziehungsweise automatisiert als für Nähsäcke. Sie benötigt daher weniger Personal, ist deutlich produktiver, aber auch kapitalintensiver.
Nähsäcke haben gerade wegen ihrer Personalintensität stark an Bedeutung verloren, halten sich aber noch immer in gewissen Märkten, in denen Personalkosten geringere Bedeutung haben oder Kleinstserien nachgefragt werden. Ein weiterer Nachteil besteht in ihrer geringeren Materialeffizienz, da die Sackwand durch die Nähnaht perforiert und damit geschwächt wird.
Abb. 10.5.2.4: genähte Säcke. Heute wird diese Produktionsmethode in Europa kaum noch eingesetzt.
Ihre Vorteile liegen in den geringen Investitionskosten für die Produktionsmaschinen, in der äußerst flexiblen Produktionsweise und in der einfachen Wiederverwendbarkeit der Säcke, da sich das Nähgarn rückstandslos und beschädigungsfrei entfernen lässt. Aufgrund der geringen Bedeutung in Europa wird an dieser Stelle auf eine detaillierte Darstellung des Fertigungsprozesses verzichtet. Im Prinzip reichen eine einfache Geradschnitt-Schlauchmaschine und ein oder mehrere Nähtische beziehungsweise Nähautomaten.
Die Herstellung von Papiersäcken erfolgt immer zweistufig: Im ersten Schritt verarbeitet die Schlauchmaschine die Papierbahnen zu Schlauchabschnitten, die im zweiten Schritt mit einer Nähmaschine, einem Pinch-, Rollboden- oder Ventilbodenleger zu Säcken konfektioniert werden. Wurden Papiersäcke zu Beginn früher noch per Hand gefertigt, so verläuft die Produktion inzwischen vollautomatisch. Dies gelang durch die Verknüpfung der Schlauchmaschine mit dem Bodenleger. Bis dahin musste die Übergabe der noch offenen Säcke an den Bodenleger per Hand erfolgen. Papiersäcke werden bereits bedruckt, bevor sie den ersten Arbeitsgang (Durchlauf der Schlauchmaschine) erreicht haben: Der Druck erfolgt entweder direkt, nachdem das Papier die Rolle verlassen hat, im sogenannten Flexo-Vorsatz-Druckwerk oder indirekt auf einer separaten Rolle/Rolle-Druckmaschine. Moderne Universal-Schlauch-maschinen können diverse Arten von Schläuchen herstellen, die sich in der Art des Zuschnitts unterscheiden:
– Geradschnitt-Schläuche
– Staffelschnitt-Schläuche
(Quelle: Gemeinschaft Papiersackindustrie e. V.)
Geklebte Kreuzboden- und Kreuzboden-Ventilsäcke
Diese Bauform macht den Hauptanteil der weltweit produzierten Papiersäcke aus. Die oben offene Version wird als Kreuzbodensack bezeichnet, die geschlossene als Kreuzboden-Ventilsack. Zu ihrer Herstellung sind eine Schlauchmaschine und ein Bodenleger erforderlich. Ventilbodenleger sind Maschinen, die sowohl Ventil- als auch oben offene Säcke produzieren können. Bei Kreuzbodenlegern wurden die Bodenklebstoffauftrags- sowie die Ventil- und Bodendeckblatt-Stationen auf einer Maschinenseite weggelassen, sodass sie nur oben offene Säcke produzieren können.
Abb. 10.5.2.5: Universal-Schlauchmaschine AM 8115 von Windmöller & Hölscher
Schlauchmaschinen
Schlauchmaschinen sind Falt-, Trenn- und Klebemaschinen, die aus rollenförmig aufgewickelten Papierbahnen in einem kontinuierlichen Arbeitsprozess ein- oder mehrlagige Schlauchabschnitte fertigen. Die Abschnitte werden je nach Lagenzahl, Papierstärke und Schlauchkonstruktion zu Paketen von etwa 20 – 100 Schläuchen gesammelt und in regelmäßigen Intervallen aus der Maschine geführt. Schlauchmaschinen werden entsprechend der Trenntechnologie für die Schlauchbahn eingeteilt in:
• Geradschnitt-Schlauchmaschinen
• Staffelschlauchmaschinen
• Staffel- und Geradschnitt-Schlauchmaschinen (Universalmaschinen genannt)
Abb. 10.5.2.6: Schlauchenden Staffelsack (links) und Geradschnittsack (rechts)
Als heutige Hochleistungs-Sackpapiere noch nicht zur Verfügung standen, wurde der Staffelschlauch beziehungsweise der Staffelsack entwickelt, um die Stabilität des Bodens und die Materialeffizienz zu verbessern. Als Säcke noch aus vier oder mehr Lagen bestanden, war letzteres ein ausschlaggebendes Argument. Dagegen steht der erhöhte Produktionsaufwand: Je nach Sortimentsstruktur musste eine Sackfabrik Dutzende bis Hunderte Sätze Staffelformate beschaffen und bevorraten, da jedes Schlauchformat einen eigenen Satz an Messer- und Querklebeplatten erfordert. Außerdem ist spezifisches Know-how zur Erarbeitung und Gestaltung der Staffelkonturen nötig, und auch bei der Produktion muss auf die Anforderungen der Staffelung Rücksicht genommen werden. Mit der Einführung von Hochleistungs-Sackpapieren und der daraus resultierenden Reduzierung der Lagenzahl hat das Argument der Materialersparnis durch Staffelung an Bedeutung verloren. Geradschnittsäcke lassen sich problemloser, schneller und mit weniger Prozessaufwand produzieren. Geradschnittsäcke benötigen aber zur Bodenverstärkung ein Bodendeckblatt; die dafür erforderlichen Aggregate sind zumindest in Europa heute Standard.
Schlauchmaschinen bestehen in der Regel aus folgenden Funktionsbaugruppen:
1 | Abwicklung mit Abwickelständern | 5 | Bahnbearbeitungsstation mit (in Laufrichtung): • Entlüftungsperforation (Nadelwalzen) • Bahnvorzügen • Abrissperforation • Querklebung • Registerwalzen • Längsklebung (optional: Daumenausschnittstation) |
2 | Bahnzuggeregelter Umfangsantrieb für das kontrollierte Abwickeln dünner Folien | 6 | Schlauchbildung |
3 | Umlenkwalzenständer | 7 | Schneid- und / oder Abreißwerk |
4 | Bahnlaufregeleinrichtung | 8 | Paketablage mit Ablagetisch |
Abb. 10.5.2.7: technologisches Schema einer W&H Schlauchmaschine.
* Druckwerke sind nicht in allen Linien integriert.
In vielen Fällen erfolgt die Schlauchproduktion bereits mit vorbedruckten Bahnen. Druckwerke werden hier je nach Bedarf inline betrieben. Alternativ dazu gibt es separate Druckmaschinen, die Rolle auf Rolle arbeiten. Die Rollen werden in diesem Fall an die Schlauchproduktion geliefert. Druckwerke kommen beispielsweise in der Zementsackproduktion zum Einsatz, wo hohe Auflagen in einfachem Druck hergestellt werden. Vorgedruckte Rollen werden in der Regel dort verwendet, wo höhere Druckqualitäten gefordert sind.
Im Folgenden werden die in der vorangegangenen Abb. 10.5.2.7 aufgeführten Baugruppen kurz dargestellt:
1. Die Aufgabe der Abwicklung besteht in der Bereitstellung der Bahnen aus dem „Arbeitsspeicher Rolle“ für die Verarbeitung. Sie besteht aus hintereinander angeordneten, seitlich um jeweils 30 mm versetzten Abwickelstellen mit je einer zusätzlichen ausschwenkbaren Wickelposition für schnelleren Rollenwechsel. Der Versatz dient dazu, die Längsnähte der einzelnen Lagen im Schlauch um diesen Betrag zu staffeln, um jede Lage mit sich selbst verkleben zu können. Jede Abwickelstelle ist mit einer Bahnbremse im Fuß des Gestells ausgerüstet, die bei einem Bahnriss oder Not-Halt die Bahnspannung innerhalb der Maschine aufrechterhält.
2. Der Umfangsantrieb (umgangssprachlich: 4-Quadranten-Antrieb) ist in der Lage, die Materialrolle mithilfe zweier angetriebener Laufräder zu beschleunigen oder abzubremsen, wahlweise in beiden Drehrichtungen. Sein Ansteuersignal bezieht er von einer Pendelwalze, die auf der Materialbahn aufliegt. Dadurch ist es möglich, die Bahnspannung zwischen dieser Abwickelstelle und dem Bahnbearbeitungsteil sehr feinfühlig zu regeln. Benötigt wird diese Funktion bei der Verarbeitung dünner und dehnbarer Materialien, wie zum Beispiel PE-HD-Sperrschicht-Folien. PE-HD ist die Abkürzung für High Density Polyethylen, also Polyethylen hoher Dichte.
3. Im Umlenkwalzenständer werden die einzelnen Lagen in ihre jeweilige Bearbeitungsebene gelenkt. Er besteht aus einem Leitwalzensatz, der in einem einfachen Gestell am Boden montiert ist.
4. Die Bahnlaufregelung gleicht seitlichen Verlauf der einzelnen Papier- oder Folienbahnen aus, der durch unregelmäßige Spannungsverteilungen im Material verursacht wird. Auf diese Weise sorgt sie für eine konstante seitliche Positionierung der Lagen relativ zu den Bahnbearbeitungswerkzeugen und damit für eine spezifikationsgerechte Schlauchgeometrie. Jede Lage verfügt bzw. besteht aus
– über ein Steuerwalzenpaar, das wie ein Fahrradlenker in der Bahnlaufebene schwenkbar ist,
– einem am Gestell angebrachten, nach Bahnbreite einstellbaren Bahnkantensensor,
– einem Auswertegerät,
– einem Stellantrieb für das Steuerwalzenpaar.
Vor dem Einlauf in die Einheit sind vertikal schwenkbare, gebogene Bügelstangen (Bananenform) angebracht, um eventuelle Falten im Material zu beseitigen.
Abb. 10.5.2.8: Bahnlaufregelung einer Vierlagen-Schlauchmaschine mit vorgeschalteten Bügelstangen
5. In der Bahnbearbeitungsstation sind alle Arbeitsschritte zusammengefasst, die an der flachen Bahn stattfinden:
Am Einlauf der Bahnbearbeitung sind häufig die Stationen für die (optionale) Flächennadelung untergebracht. Die Flächennadelung wird nicht bei allen Säcken durchgeführt. Das ist von den Kundenwünschen und der Sackbauart abhängig. Oben offene Säcke oder Ventilsäcke aus hochporösem Papier werden in der Regel nicht genadelt. Die Stationen für die Flächennadelung bestehen jeweils aus einer Nuten- oder Bürstenwalze, über die die Bahn läuft, sowie einer nicht angetriebenen Nadelwalze. Die Flächennadelung dient dazu, die Bahn mit Entlüftungslöchern zu versehen. Je nach gewünschter Luft-Durchsatzrate kann die Besatzdichte der Walzen variieren; üblich sind 12,5 x 12,5 mm oder 25 x 25 mm Nadelabstand. Bei Verwendung kegeliger Nadeln besteht die Möglichkeit, die Entlüftungsleistung durch die Wahl der Einstechtiefe zu verändern, da dies die Lochgröße bestimmt. Zur schnellen Veränderung des Nadelbildes ohne zeitaufwendigen Tausch der Nadelwalzen sind manche Maschinen mit drehbaren Halterungen („Revolver“) ausgestattet, die jeweils bis zu vier verschiedene Nadelwalzen aufnehmen können. Moderne Schlauchmaschinen verfügen darüber hinaus über eine „Skip-Perforation“-Funktion, bei der die Nadelwalzen taktweise (das heißt: einmal pro Abschnitt) von der Bahn abgehoben werden. Die Abhebung ist so synchronisiert, dass die Bahn im Bereich des Querklebeauftrags nicht perforiert wird. Das unterbindet einen eventuell störenden Durchschlag des Klebstoffs durch die Löcher nach innen oder außen.
Abb. 10.5.2.9: Flächennadlung mit zwei Nadelwalzen in Vierfach-Revolverhalterung. Die spiralige Nadelanordnung sorgt für einen unterbrechungsfreien Eingriff und damit für einen gleichmäßigen Lauf. Die gesamte Einheit ist innerhalb der Maschine seitlich verstellbar, um die Position des Nadelbilds einzustellen.
Unmittelbar nach der Flächennadelung folgen die Bahnvorzüge. Sie ziehen die Bahnen von der Rolle bis in den Bahnbearbeitungsteil und sorgen gemeinsam mit dem Hauptvorzug der Maschine im Schneid- / Abreißwerk dafür, die Bahnspannung im Bahnbearbeitungsteil aufrechtzuerhalten. Aufgebaut sind sie als förderwirksames, angetriebenes Walzensystem pro Lage – entweder als Friktionsvorzug oder als drehmomentgeregelter Walzenspalt-Vorzug mit Bahnzugsensor und Direktantrieb.
Abb. 10.5.2.10: Friktionsvorzug. Die Position der einstellbaren Pendelwalze bestimmt das Maß der Umschlingung der angetriebenen Vorzugwalze und damit den Betrag der Friktion (Reibung) zwischen Bahn und Walze. Je höher die Friktion, desto höher ist der Fördereffekt des Systems.
In der darauffolgenden Perforationsstation wird jede Bahn mit einer quer verlaufenden Abrissperforation versehen, die entweder einer geraden oder konturierten (gestaffelten) Schnittlinie folgt. Pro Lage besteht die Station aus einer angetriebenen Werkzeugwelle (Formatwelle) und einer nicht angetriebenen Gegenwalze (geriffelte Stahl- beziehungsweise Bürstenwalze). Die Formatwelle nimmt die vorkonfigurierte austauschbare Messerplatte (Formatplatte) auf – diese besteht aus einem Aluminium-Trägerprofil mit darauf montierten Messersegmenten. Die damit erzeugte Schnittkontur richtet sich nach dem Schlauchformat und dem gewünschten Staffelverlauf. Die Messer bestehen aus gezahnten Klingen, deren Zähne durch das Material in die Nuten der Riffelwalzen oder in die Bürstenwalze stechen. Zur Synchronisation der Messergeschwindigkeit mit der Bahngeschwindigkeit bei unterschiedlichen Schlauchlängen werden entweder Kurbelschleifengetriebe verwendet, die die Messer für die Zeit des Einstichs auf Bahngeschwindigkeit bringen, oder Durchmesser-variable Perforationseinheiten, bei denen Umlauf- und Bahngeschwindigkeit stets gleich sind.
Abb.10.5.2.11: Abrissperforation. Umlaufende Messerplatte oberhalb, geriffelte Gegenwalze (Nutenwalze) unterhalb der Bahn
Nach der Perforation gelangen die Bahnen zur Querklebung. Da mit einer Klebung zwei Bahnen miteinander verbunden werden, reicht es aus, die Querklebestation einer vierlagigen Schlauchmaschine nur mit drei Querklebeeinheiten auszustatten. Jede Einheit bringt vor und hinter der Perforationslinie quer zur Bahn jeweils eine Klebepunktlinie auf, um die Bahnen im Kopf- und Fußbereich des Schlauches zu verkleben. Die Verklebung dient dazu, die Schlauchenden im Bodenleger mithilfe von Gummisaugern aufziehen zu können. Sie dient auch dazu, das Eindringen von Füllgut zwischen die Lagen während des Abfüllprozesses zu verhindern. Schlussendlich geht es bei oben offenen Säcken auch darum, dass sich der Sack leicht öffnen lässt.
Jede Einheit besteht aus einer angetriebenen Werkzeugwelle (Formatwelle) mit dem darauf aufgespannten Querklebewerkzeug sowie einem Klebstoffauftragswerk, das durch die angetriebenen Klebe- und Dosierwalzen sowie das Klebstoffbecken oder die Spritzwanne gebildet wird. Bei einfachen Maschinen erfolgt die Versorgung des Querklebewerkzeugs über die Dosierwalze aus dem Becken; modernere Maschinen verfügen über ein wannenloses Klebstoffauftragswerk, bei dem sich der Klebstoff im Walzenspalt befindet; die Wanne dient hier nur der Spritzeraufnahme sowie zu Waschzwecken. Von der Auftragswalzenoberfläche nimmt das Querklebewerkzeug den Klebstoff ab und überträgt ihn auf die Bahn.
Abb.10.5.2.12: Querklebestation – umlaufender Werkzeugträger mit aufmontiertem Querklebewerkzeug (Querklebeplatte in Tupferversion). Die aufgesteckten Gummitupfer (schwarz) erzeugen die Klebekontur.
Das Werkzeug selbst besteht analog zum Perforationswerkzeug aus einer vorkonfigurierten austauschbaren Querklebeplatte (Formatplatte), die aus einem Aluminium-Trägerprofil mit darauf montierten Übertragungselementen aufgebaut ist. Anstelle von Formatplatten mit fest montierten Klebeelementen werden heute häufig solche verwendet, die mit einer Matrix aus Trägerbolzen für die Aufnahme von Gummitupfern bestückt sind, da sie eine schnelle Veränderung der Klebekontur erlauben.
Abb. 10.5.2.13: Auftragssystem mit Klebstoffwanne (links), wannenloses Auftragssystem (rechts)
Im Gegensatz zur Perforation besteht in der Querklebung nicht die Notwendigkeit einer exakten Synchronisation von Bahn- und Werkzeuggeschwindigkeit, da die Querklebetupfer die Bahn nur berühren. Geschwindigkeitsdifferenzen führen nur zu einer Verbreiterung des Querklebepunktes und können in gewissem Umfang toleriert werden.
In neuerer Zeit sind die vorbeschriebenen Versionen des „analogen“ Klebstoffübertrags durch rechnergesteuerte Düsensysteme ersetzt worden. Diese ersparen die Beschaffung, Anfertigung und Lagerung der Querklebe-Formatteile, verkürzen die Formatumstellung und erzeugen einen wesentlich präziseren Klebstoffauftrag – sowohl hinsichtlich der Menge als auch der Platzierung.
Abb. 10.5.2.14: Düsenbalken mit Steuerventilen einer digitalen Querklebung
Abb. 10.5.2.15: Klebstoffauftragsbild (Demo-Version) einer digitalen Querklebung
Vor dem Einlauf in die Längsklebung sind die Registerwalzen angeordnet. Es handelt sich dabei um pendelnd aufgehängte Leitwalzen, deren Stellung sich über eine Verstellspindel justieren lässt. Ihr Zweck besteht darin, die Länge des Bahnwegs zwischen den Orten des Quer- und des Längsklebeauftrags so zu verändern, dass auch bei Dehnungen oder Längungen einzelner Bahnen die Perforationslinien im fertigen Schlauch deckungsgleich übereinander liegen. Nach dem Passieren der Registerwalzen werden die Lagen aufeinander gelegt, sodass die Querklebepunkte in Kontakt mit der benachbarten Bahn kommen und die Verklebung beginnt. Die Längsklebung überträgt durchlaufende oder im Bereich des Schlauchendes unterbrochene Klebstoffspuren von rund sechs Millimetern Breite, jeweils in geringem Abstand zur Längskante der Bahn. Da die Lagen bereits in der Abwicklung um 30 Millimeter seitlich versetzt wurden, beträgt auch der Abstand der Klebstoffspuren voneinander 30 Millimeter. Die Station besteht aus einem Klebstoffauftragswerk und einer seitlichen Verschiebeeinrichtung zur Anpassung des Klebstoffauftrags an unterschiedliche Schlauchformate. Das Klebstoffauftragswerk verfügt über eine Klebstoffwanne, eine angetriebene Schöpf- und Auftragswalze, eine Dosierwalze und die angetriebene Klebstoffscheibenwelle, auf die ein Satz Klebstoffauftragsscheiben als austauschbares Formatteil aufgesteckt werden kann. Die Anzahl der Klebstoffauftragsscheiben im Satz richtet sich nach der Lagenzahl. Anstelle des Klebstoffauftragswerks kann heute auch ein Auftragsdüsenblock Verwendung finden.
Abb. 10.5.2.16: Registerwalze (oben) und Längsklebung, hier ausgestattet mit vier Klebstoffscheiben mit Lücke zur Unterbrechung des Auftrags im Bereich des Schlauch-Endes
Sollen mit der Schlauchmaschine auch Schläuche für oben offene Säcke gefertigt werden, so ist sie meist mit einer Daumenausschnittvorrichtung ausgestattet. Diese stanzt einen halbmondförmigen Ausschnitt von ca. 30 mm Durchmesser in die vordere Schlauchwand. Der einseitige Ausschnitt erleichtert die manuelle Öffnung des Sack-Endes für die Befüllung. Die Station besteht aus einem umlaufenden Stanzwerkzeug und dem ebenfalls umlaufenden Gegenstück. Zur Synchronisation von Bahn- und Messergeschwindigkeit bei unterschiedlichen Schlauchlängen kommen entweder Kurbelschleifengetriebe oder durchmesser-veränderliche Stationen zur Anwendung. Statt des Daumenlochwerkzeugs kann auch ein Nadelwerkzeug in die Station eingesetzt werden, mit dem die gesamte Schlauchwand auf einer definierten Fläche (meist unterhalb des Ventils) von innen nach außen durchstoßen werden kann, um die Entlüftungsleistung des Sackes zu erhöhen.
Abb. 10.5.2.17: Flachschlauchbildung, Blick gegen die Laufrichtung. Im Hintergrund sind die Einlaufwalzen zu erkennen.
6. In der Schlauchbildung erfolgt die Längsfaltung der Flachbahn und die Verklebung zum Schlauch, indem die seitlichen Überstände der Bahn um zwei in Längsrichtung angeordnete Bleche geschlagen werden und die Längsklebung in Kontakt mit der gegenüberliegenden Schlauchseite kommt. Die Schlauchbildung ist ein passives (antriebsloses) System und besteht aus vertikalen Schlauchbildungsholmen mit daran befestigten Einlaufwalzen und inneren Schlauchbildungsblechen sowie Führungsrollen und Stäben, die außen auf den Schlauch aufgelegt werden können. Seitenfalten-Schlauchbildungen sind auf jeder Seite mit zwei übereinander liegenden inneren sowie einem äußeren Blech ausgestattet.
7. Das Schneid- und/oder Abreißwerk trennt die Schlauchbahn in Abschnitte von definierter Länge. Die Trennung erfolgt entweder durch Abriss entlang einer Perforationslinie oder durch einen Schnitt. Die Einheit besteht aus folgenden Unterbaugruppen:
• Der Hauptvorzug ist ein permanent wirkender, förderwirksamer Walzenspalt, der die Schlauchbahn durch die Maschine zieht. Er ist als doppeltes, angetriebenes Walzen- oder einfaches Bänderpaar aufgebaut.
• Der Abreißvorgang ergibt sich aus dem Zusammenwirken von Festhalte- und Abreißwalzen beziehungsweise Bändervorzug und Bänderabreißer. Die Festhaltewalze (nur bei Walzensystemen) ist ein zeitweise wirkender, förderwirksamer Walzenspalt, aufgebaut als einfaches, angetriebenes Walzenpaar. Seine Umfangsgeschwindigkeit ist geringfügig kleiner als die des Hauptvorzugs, um ein Durchrutschen des Schlauchs im Hauptvorzug während des Abrisses zu verhindern. Die Abreißwalze ist analog zur Festhaltewalze beziehungsweise dem Bändervorzug aufgebaut, läuft jedoch mit einer etwa 20 Prozent höheren Geschwindigkeit. Der Abriss erfolgt dadurch, dass die abgehobenen Festhalte- und Abreißwalzen gleichzeitig kurz an die Bahn angedrückt werden. Dabei übt die höhere Geschwindigkeit der Abreißwalze Zugkräfte auf die Schlauchbahn aus, die die Trennung bewirken. Die Andrück-Bewegung der Festhalte- und Abreißwalzen wird durch je eine Exzenterscheibe gesteuert.
• Zwischen Festhalte- und Abreißwalze ist üblicherweise eine Abreißhilfe eingebaut. Sie besteht aus quer eingebauten Laufkörpern, die die Bahn zwischen Festhalte- und Abreißwalze geringfügig umlenken und lokal die Zugspannung erhöhen. Alternativ kann hier auch ein Schneidsystem für den Geradschnitt eingebaut sein, das aus einem oben liegenden Messer-Rotor und einem unten liegenden Gegenkörper besteht.
• Auswerferbänder, die aus angetriebenen Bänderpaaren bestehen und mit Abreißergeschwindigkeit betrieben werden, dienen zum Herausführen der vereinzelten Schlauchabschnitte auf das Schuppen-Transportband der Paketablage.
Abb. 10.5.2.18: Walzenabreißwerk (Papierlaufrichtung von rechts nach links)
Abb. 10.5.2.19: Bänderabreißwerk (Papierlaufrichtung von rechts nach links)
8. In der Paketablage findet die Bildung von Schlauchpaketen zur Übergabe in den nachfolgenden Prozess statt. Auf dem langsam laufenden Schuppentransportband werden die Schläuche mit einem Versatz von einigen Zentimetern abgelegt und bis in die Paketsammelbox transportiert, wo sie sich vor einer schwenkbaren Anschlagklappe zum Paket aufstauen. Nach Erreichen einer voreingestellten Schlauchanzahl wird der Kopf des Schuppenstroms auf dem Schuppenband kurzzeitig angehalten, sodass sich die ankommenden Schläuche etwas zusammenschieben. Während dieser Zeit kann die Paket-Anschlagklappe geöffnet, das Paket abtransportiert und die Klappe für den nächsten Sammelzyklus wieder geschlossen werden.
Bodenleger
Bodenleger sind Falt- und Klebemaschinen, die aus paketweise angelieferten Schlauchabschnitten verwendungsfähige oben offene Säcke oder Ventilsäcke aus Papier herstellen. Die fertigen Säcke werden zu Paketen von zehn bis 25 Sack gesammelt und in regelmäßigen Intervallen aus der Maschine geführt.
Abb. 10.5.2.20: Ventilbodenleger AD 8330 (Quelle: Windmöller & Hölscher)
Bodenleger werden entsprechend ihrem vorgesehenen Verwendungsschwerpunkt mit unterschiedlichen Formatbereichen gebaut. Wesentlichen Einfluss hierauf nimmt die Stationslänge (auch: Taktlänge); sie wird durch den Umfang der Werkzeuge (zum Beispiel Rillkörper, Klebstoffklischeezylinder, Zangenzylinder) definiert.
Da der Werkzeugumfang (= Stationslänge) immer einer Sackbreite plus einer Lückenbreite entspricht, ist damit auch die maximale Sackbreite festgelegt. Eine minimale Lückenbreite von etwa zwei bis drei Zentimetern ist erforderlich, um die Säcke mithilfe elektrooptischer Sensoren voneinander unterscheiden zu können.
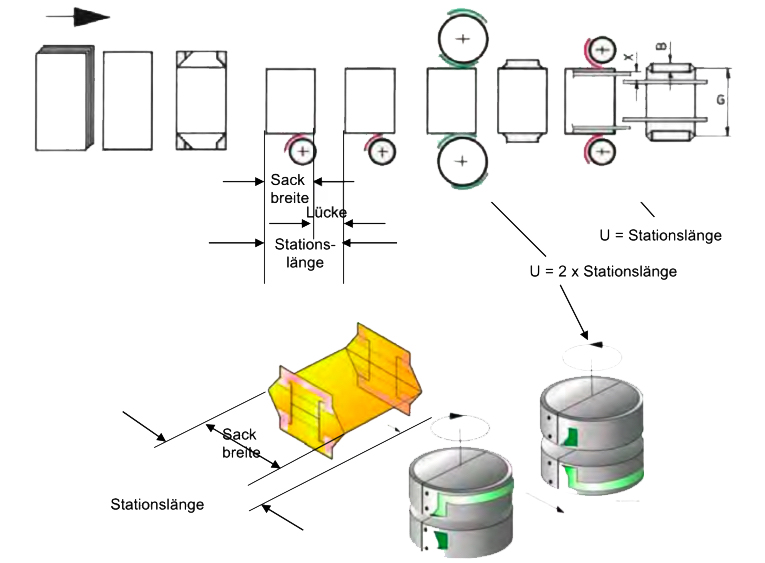
Abb. 10.5.2.21: Abbildung von in der Sackproduktion wichtigen Maßen. Die Größe „G“ (in der Abb. oben rechts) bezeichnet den „Bodenmittenabstand“. Er ist durch Verschieben der Antriebsseite des Bodenlegers gegenüber der feststehenden Bedienungsseite in einem gewissen Bereich veränderbar (siehe auch Abschnitt 3 „Transportsystem“).
Die Stationslänge (auch Takt beziehungsweise Taktlänge) ist eine konstruktiv festgelegte Größe. Sie bildet sich aus der Summe von Sackbreite und Lücke. Wenn eine kleinere Sackbreite gefahren wird, ist die Lücke größer und umgekehrt. Die maximale Sackbreite ergibt sich also aus der Stationslänge minus Mindestlücke. „Großformatige“ Bodenleger verfügen daher über eine größere Taktlänge als kleinformatigere. Da die Taktlänge nur die maximale Sackbreite begrenzt, ist damit allein keine Aussage über das Sackvolumen möglich, weil es darüber hinaus von Sacklänge und Bodenbreite abhängt. Ein spezifisches Sackvolumen (zum Beispiel 35 Liter) lässt sich durch eine Vielzahl von Kombinationen dieser drei Parameter darstellen. Sie werden so ausgewählt, dass das konkrete Sackformatweitere Anforderungen erfüllt, insbesondere das Palettenmaß einhält. Die Stationslänge beeinflusst aber auch die Leistung des Bodenlegers. Wenn man unterstellt, dass die Transportgeschwindigkeit durch maschinenbauliche Faktoren begrenzt wird, ergibt sich aus einer größeren Taktlänge eine geringere maximal mögliche Geschwindigkeit in Stück pro Minute als bei Wahl einer kleineren Taktlänge.
Beispiel
Maximale Transportgeschwindigkeit 220 m/min:
Bei Taktlänge 754 mm: 220 m/min : 0,754 m = 291 Stück/min
Bei Taktlänge 635 mm: 220 m/min : 0,635 m = 346 Stück/min
In beiden Fällen läuft der Transport des Bodenlegers gleich schnell, es kommen aber unterschiedliche Produktionsmengen pro Zeiteinheit heraus.
Die Wahl der Taktlänge ist also eine der wichtigsten Entscheidungen bei der Ausrichtung der Konstruktion eines Bodenlegers auf ein bestimmtes Marktsegment. Wichtig für den Kunden sind der Formatbereich, der sich nach seinem Sortenprogramm richtet, und natürlich die Leistung in Stück.
Transportgeschwindigkeit und Taktlänge sind zwar die dafür maßgeblichen Faktoren, interessieren ihn aber erst in zweiter Linie.
Die folgende Grafik veranschaulicht die Bearbeitungsabfolge auf einem Ventilbodenleger:
Abb. 10.5.2.22: Bearbeitungsabfolge auf einem W&H Ventilbodenleger
Erläuterung zu Abb. 10.5.2.21:
1. Vereinzelung der Schläuche aus dem Schlauchpaket
2. Rechtwinklige, lage- und phasenrichtige Ausrichtung der Einzelschläuche
3. Prägung von Bodenmitten- und Dreieckstaschenfalz, optional Einschnitt der Bodenklappen und Kissennadelung
4. zweiphasige Bodenöffnung durch umlaufende Sauger und mechanische Spreizelemente
5. Aufkleben eines einfachen oder doppelten Zettels (als Teil des Ventils) auf eine Dreieckstasche im Scharnierapparat; für einfachere Ventile kann dieser Schritt/diese Station weggelassen werden.
6. Aufkleben eines einfachen oder doppelten Zettels (als weiterer Teil des Ventils) auf das Scharnier im Ventilapparat. Aufbau und technologischer Ablauf im Scharnier- und Ventilapparat ähnlich dem der Schlauchmaschine.
7. Klebstoffauftrag auf die geöffneten Bodenklappen durch ein dem Hochdruckprozess vergleichbares Verfahren oder mithilfe einer Düsenmatrix
8. Falten der Bodenklappen nacheinander um jeweils 180° zum geschlossenen Boden durch Vorbeilaufan entsprechend gestalteten Stäben und Blechen
9. Aufkleben jeweils eines Verstärkungszettels (Bodendeckblatt) auf die geschlossenen Böden durch die Bodendeckblattapparate (Option); Aufbau und technologischer Ablauf in den Apparaten sind vergleichbar mit einem Scharnier- und Ventilapparat.
10. Wenden der Sackböden um 90° (Flachlegung) mit anschließendem Pressen zum Zweck des Ausbildens einer möglichst dichten Verklebung. Das Pressen überwindet die Rückstellkräfte des Papiers so lange, bis der Klebstoff eine ausreichende Klebwirkung ausgebildet hat.
11. Zählen und Paketieren der fertigen SäckeIm Folgenden werden die Baugruppen zu den bereits erläuterten Verfahrensschritten kurz dargestellt:
1. Rotationsanleger
Abb. 10.5.2.23: Rotationsanleger (links) – Blick durch den Paketaufnahmeschacht auf den Rotor (rechts)
Im Rotationsanleger werden die Schläuche aus dem Schlauchpaket vereinzelt und nacheinander an den Schlauchausrichter übergeben. Da jeweils der unterste Schlauch aus dem Paket abgezogen wird, können immer wieder neue Pakete nachgelegt und damit ein kontinuierlicher Betrieb des Bodenlegers sichergestellt werden. Der Anleger besteht aus dem Gestell, dem darin liegenden Rotor mit Planetenradantrieb, acht Saugtrommeln und der Saugluftsteuerung sowie dem Bänderzylinder. Das notwendige Vakuum wird durch eine separate Pumpe aufgebracht. Durch die Rotation des Rotors und die gleichzeitige gegenläufige Rotation der Saugtrommeln auf dem Rotor ergibt sich eine Bewegung, die die einzelnen Sauger auf einer Zykloidenkurve führt.
Abb. 10.5.2.23: Zykloide Kurven. Die Zykloide ist eine Kurve, die von einem festen Punkt auf einem Kreis gezeichnet wird, der auf einer Geraden abrollt. Mehr: https://www.mathi.uni-heidelberg.de/~thaeter/anasem08/02Spezielle%20Kurven_01_11_2008.pdf
In den Umkehrpunkten der Zykloide steht der Sauger für einen sehr kurzen Moment still, sodass der unterste Schlauch des Pakets angesaugt und nach kurzem Weitertransport wieder freigegeben werden kann. Der Bänderzylinder führt die Schläuche dann aus dem Anleger und wirft sie auf den Schlauchausrichter.
Abb. 10.5.2.24: Bewegungsablauf Rotationsanleger. Rot: Zykloide. Ausschnittvergrößerung rechts: Bänderzylinder
2. Schlauchausrichter
Abb. 10.5.2.25: Schlauchausrichter (links) und Funktionsschema (rechts)
Diese Station hat die Aufgabe, die Schläuche rechtwinklig zur Maschinenlängsachse sowie lagerichtig zur maschinenfesten Referenzlinie und synchron zu den Bearbeitungsstationen auszurichten. Damit werden die Voraussetzungen für eine rechtwinklige Geometrie des Sackes, für korrekte Bodenbreite und die richtige Position der Nadelungen, Rillungen, Einschnitte, Klebungen und der Zettel geschaffen.
Der Ausrichter besteht aus einem Ausrichtetisch mit mehreren darauf laufenden, parallel angeordneten Zahnriemen mit vertikalen Anschlägen, die etwa im Abstand einer Stationslänge angebracht sind. Zwischen den Zahnriemen verläuft ein Transportbändersystem, das in Laufrichtung leicht schräg angeordnet ist und aus mehreren, parallel angeordneten Ober- und Unterbändern (Habasitbändern) besteht. Ein weiteres vertikal angeordnetes Ausrichteband bildet die Begrenzung zur Bedienungsseite.
Die Habasit Holding AG mit Sitz in Reinach ist ein international tätiger Schweizer Hersteller von Antriebsriemen und Transportbändern. Diese bestehen im vorliegenden Fall aus Gummi mit hoher Haftreibung. Mehr: www.habasit.com
Der Ausrichter fördert die Schläuche mittels der schräg angeordneten Habasitband-Paare mit einer etwas höheren Geschwindigkeit als die Ausrichtezahnriemen. Dadurch werden die Schläuche gleichzeitig gegen die Zahnriemenanschläge und in Richtung Bedienseite gegen das vertikale Ausrichteband geschoben.
3. Transportsystem
Das Transportsystem (kurz: der Transport) erstreckt sich vom Auslauf des Schlauchausrichters bis zur Ausschussweiche und transportiert die Schlauchabschnitte beziehungsweise Säcke durch die Maschine.
Abb. 10.5.2.26: Transportschema (Draufsicht). Rot dargestellt sind die Transportriemen. Die in Laufrichtung linke Maschinenseite ist zur Veränderung der Sacklänge komplett verschiebbar angeordnet. Der Versprung des Transportes am Ende der Maschine ermöglicht das Umlegen der Böden.
Abb. 10.5.2.27: oberes Transportsystem mit einzeln auswechselbaren, federnd gelagerten Transportrollen, die den Transportriemen führen.
Die Säcke werden zwischen Transportriemenpaaren auf Antriebs- und Bedienseite eingespannt und befördert. Während der untere Transport fest eingebaut ist, liegt der obere federnd gelagert auf den Säcken auf. Durchmessereinstellbare Riemenscheiben (sogenannte Spreizscheiben) treiben die Riemen an und können zur Synchronisation aller vier Riemen entsprechend eingestellt werden.